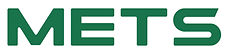

The SKF Bearing Life Cycle
Every bearing has a pre–calculated service lifetime. However, research has shown that for various reasons, not every bearing achieves it. Important stages, which have a major impact on a bearing service lifetime can be recognised during the bearing’s lifecycle. These stages are mounting and lubrication, alignment, re–lubrication, basic condition monitoring and dismounting.
The stages in a bearing life cycle are extremely important for achieving the maximum service life of the bearing.
By applying the right maintenance practices and using the correct tools, you can considerably extend your bearing’s service life and increase plant productivity and efficiency.
Mounting and lubrication
Includes mechanical fitting tools, induction heaters, and hydraulic equipment.
Mounting is one of the critical stages of the bearing’s lifecycle. If the bearing is not mounted properly using the correct method and tools, the bearing’s service lifetime will be reduced. Lubrication is also an important step in the mounting procedure. Selecting bearing grease suitable for the application is critical to achieving optimum performance. Additionally, the quantity of grease and the lubrication method used can positively influence the service life of the bearing.
Alignment
Includes shaft and belt alignment tools and machinery shims.
After the bearing has been mounted in an application,such as a motor connected to a pump, the application should be aligned. If the application is not properly aligned, the misalignment can cause the bearing to suffer additional load, friction and vibration. These can accelerate fatigue and reduce the bearing’s, as well as other machine components, service life. Furthermore, increased vibration and friction can significantly increase energy consumption and the risk of premature failures.
Re–lubrication
Includes bearing greases, manual and automatic lubricators and lubrication accessories.
When operating, the bearing requires correct re–lubrication practices to optimise its performance. Selecting bearing grease suitable for the application and applying the right quantities at correct intervals are essential for achieving the maximum service life of the bearing. Additionally, the re–lubrication method used can positively contribute to optimising the bearing’s service life. Continuous lubrication using automatic lubricators, single or multiple–point, provides more consistent, correct and contamination–free grease supply than manual re–lubrication methods.
Basic condition monitoring
Includes temperature, noise, speed and vibration measuring instruments.
During operation, it is important to regularly inspect the condition of the bearing by performing basic condition monitoring, such as temperature, vibration and noise measurements. These regular inspections will allow the detection of potential problems and help to prevent unexpected machine stops. Consequently the machine maintenance can be planned to suit the production schedule, increasing the plant’s productivity and efficiency.
Dismounting
Includes pullers, both mechanical and hydraulic, induction heaters and hydraulic equipment.
At some point, the bearing will reach the end of its service life and will have to be replaced. Although the bearing may not be used again, it is extremely important to dismount it correctly so that the service life of the replacement bearing is not compromised. Firstly, the use of proper dismounting methods tools will help prevent damage to other machine components, such as the shaft and housing, which are often re–used. Secondly, incorrect dismounting techniques can be hazardous to the operator.




